Table Of Content

In the end, these tools help engineers optimize designs, anticipate performance and evaluate manufacturability. This allows for quicker time-to-market, lower costs and better product quality. Design for manufacturing (DFM) contributes to product innovation and efficiency by integrating manufacturing considerations into the design process. This approach allows for the identification and elimination of potential manufacturing constraints early on, fostering innovation through more feasible designs. By optimizing designs for manufacturing, DFM enhances efficiency by streamlining production processes and reducing costs. Such an advanced manufacturing simulation was once a pipe dream due to the lack of available tools and manufacturing processes.

The Key Role of the Manufacturing Cost Modeling Software in Fact-Based Negotiations
Most importantly, we'll be able to achieve more sustainable, efficient and agile engineering methods in the future. By standardizing procedures, terms and design principles, you can reduce ambiguity and maximize clarity, which in turn facilitates effective teamwork and problem resolution. Other possible obstacles include minimizing costs, making the most efficient use of materials and balancing design goals with manufacturing constraints.
What You Need to Know About Gate-All-Around Designs
Early collaboration can significantly reduce production costs and lead times. It can also improve product quality and reliability by ensuring that the product is designed with manufacturing best practices in mind. Moreover, early collaboration fosters better communication and understanding between design and manufacturing teams, leading to more efficient and effective product development processes. DFM occurs early in product development, before tooling and the assembly process, when the product is being designed.
A platform for growth: DfMA and virtual prototyping for Everton Stadium - Buro Happold
A platform for growth: DfMA and virtual prototyping for Everton Stadium.
Posted: Wed, 24 Apr 2024 16:39:54 GMT [source]
Hair
Buyers seeking quotes for parts are responsible for defining the specific requirements for those parts. CAD tools analyze material choices, part orientation, tooling needs, and production tolerances to include DFM concepts. Furthermore, CAD models can be translated into machine instructions for CNC (Computer Numerical Control) mills and 3D printers using computer-aided manufacturing (CAM) software. This enables virtual testing and process optimization of manufacturing procedures before the start of actual production.
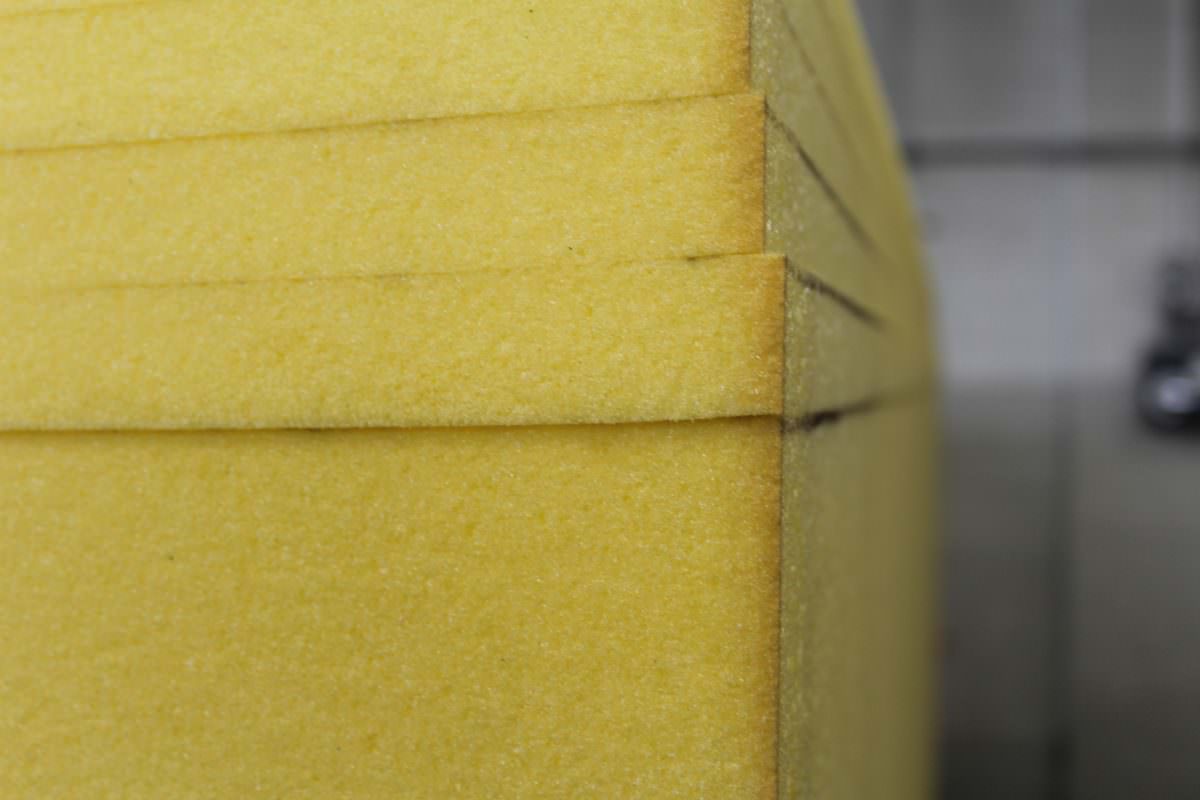
Any commercial design process is presumably conducted with at least some attention to how the underlying product will ultimately be produced. But design for manufacturability has evolved into a more formalized, analytical approach to this underlying concern—a dramatic break from historical practices. Embracing cloud technology in the wake of the supply chain crisis induced by COVID-19 is not merely a stopgap measure but a strategic evolution. By merging design and manufacturing more closely than ever, companies can achieve greater efficiency and adaptability. This shift is essential for building more resilient supply chains capable of withstanding future challenges and capitalizing on new opportunities in an unpredictable global market.
Design for manufacturing and assembly (DFMA), is an engineering methodology that focuses on simplifying the design of a product to improve ease of manufacture and efficiency of assembly. DfMA is a design methodology that emphasises manufacturing simplicity and assembly efficiency. As a result, a product’s design can be improved to enable faster, safer, more cost-effective, and more efficient manufacturing and assembly. Ultimately, DFM is a collaborative effort that benefits significantly from the expertise of all involved parties. By recognizing and leveraging the insights of suppliers, businesses can make DFM a more effective strategy, improving their overall product development process. In Design for Manufacturing, suppliers also play a crucial role, as they have expertise and deep knowledge about their specific processes and materials.
Design for Manufacturing refers to the practice of designing products in a way that optimizes their manufacturability. The primary goal is to minimize production costs, reduce complexity, and ensure product reliability while adhering to quality standards. This involves making decisions in the design phase that will simplify the production process, like choosing readily available materials, reducing the number of parts, and considering ease of assembly. Thus, designing products using DFM creates a solid plan for product development before the design process even begins.
What are the best tools to use for DFM?
In other words, the transistor can access its current more easily through this less resistive topology. This approach eliminates the need for extensive power resource allocation on the top side of the die; therefore, the metal scheme can be simplified and the resources reallocated and optimized for signal routing. These changes can simultaneously improve an SoC’s ability to distribute power, reduce IR-drop, and significantly help improve routability. In this video, discover how Carrier uses aP Design to deploy and conduct late-stage cost modeling as its going through the traditional gates such as the PLM as well as the design process. APriori helps Carrier innovate and validate new value streams efficiently and cost-effectively.
They are only made by a select group of companies, partly due to the need for specialist welding techniques. The company had been waiting for the outcome of an ongoing SMR design competition in the UK – first announced by the Government in 2015 – before it made a decision on the pressure vessel plant. The FTSE 100 company had originally proposed one factory to make heavy pressure vessels for its SMRs and another to make the building blocks of the reactors. Rolls-Royce has scaled back plans to build two new factories for its small modular reactor (SMR) programme in the UK, following delays to a government design competition. Today’s announcement is part of Toyota’s commitment to increase electrification efforts in the U.S. and grows the company’s total investment in its Indiana facility to $8 billion.
This long-term investment that began on the mobile-first foundations of the Android Open Source Project has produced a full mixed reality operating system used by millions of people. Toyota directly employs more than 63,000 people in North America who have contributed to the design, engineering, and assembly of nearly 47 million cars and trucks at our 13 manufacturing plants. By 2025, Toyota’s 14th plant in North Carolina will begin to manufacture automotive batteries for electrified vehicles.
Carrier wanted to break down manufacturing siloes and empower their engineering team to leverage the power of aPriori to streamline should costs and quotations without interrupting or delaying the design process. Design for assembly refers to designing a product to maximize how easily it can be assembled and disassembled for repairs and maintenance. This approach often focuses on principles like minimizing the total number of parts used, ensuring that parts are easily insertable, and confining assembly requirements to simple, repetitive motions. However vital, design for manufacturability is only one part of the puzzle when it comes to optimizing product costs and lowering the carbon footprint. Learn more about how to optimize product cost engineering for your organization.
No comments:
Post a Comment